ARTS ENERGY économise de précieux kWh
Le spécialiste des batteries rechargeables ARTS ENERGY a engagé une ambitieuse démarche d’efficacité énergétique. Cette PME installée à Nersac (16) poursuit ses efforts après l’obtention de la certification ISO 50001.
Fab équipements électriques et électroniques
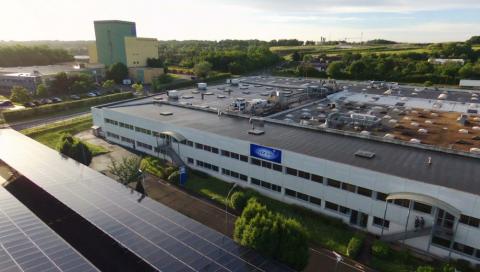
Réduire les consommations électriques
Un ambitieux programme d’efficacité énergétique en vue d’abaisser les consommations électriques a été lancé depuis 18 mois par cette PME de 220 salariés (36 millions € de CA en 2018).
L’obtention de la certification ISO 50001 en novembre 2019 est venue couronner ce vaste chantier. Mais celui-ci n’est pas pour autant achevé.
Pourquoi cet industriel extrêmement sollicité par les marchés du médical, du solaire, de l’électronique, de l’éclairage et de la défense, a-t-il choisi d’embrasser cette approche exigeante ? Tout d’abord, Arts Energy avait l’obligation de conduire tous les quatre ans un audit énergétique, comme les 5 000 entreprises françaises concernées par la directive européenne sur l’efficacité énergétique de 2012*. Cette contrainte règlementaire a poussé son comité directeur à engager une réflexion plus globale.
En effet, la concurrence musclée imposée par les fabricants asiatiques incite la société à se maintenir constamment à la pointe dans son secteur. À ce titre, elle consacre 4 % de son chiffre d’affaires à la recherche et développement. Ainsi, en s’engageant dans l’ISO 50001, son ambition consiste à déployer un véritable système de management de l’énergie ; une démarche plus efficiente à long terme qu’un simple audit et valorisable par ailleurs sur le plan commercial grâce à la certification. Enfin, ce processus prolonge l’engagement d’Arts Energy dans la démarche de “Territoire à énergie positive” portée par la région Nouvelle Aquitaine
Démarche partenariale
Les résultats ont déjà été palpables sur l’exercice 2019, avec une baisse de 12,3 % de la consommation électrique, soit une économie annuelle approchant un gigawattheure. «Nous sommes d’autant plus satisfaits qu’une partie importante de ce gain a été obtenue sur les quatre derniers mois de l’année. On peut donc considérer que cette économie peut être multipliée par deux dans le cadre d’un fonctionnement normal de l’usine», pointe Manuel Alonso, Responsable Maintenance et référent énergie de l’entreprise. Le programme a toutefois dû tenir compte de l’implantation particulière de l’usine. Arts Energy partage en effet ses locaux avec l’entreprise SAFT dont il s’est dissocié en 2013. Cette filiale du groupe Total lui loue 17 000 m2 d’ateliers, lui fournit une partie des électrodes nécessaires à la conception des accumulateurs, ainsi que la totalité de ses énergies. Les investissements dans de nouveaux équipements ont donc été cofinancés par Arts Energy à hauteur de ses consommations annuelles.
L’état des lieux des consommations énergétiques réalisé en amont, grâce à l’installation de compteurs électriques, a permis de hiérarchiser les priorités. Dans le détail, l’électricité représente 64 % de ses besoins en énergies et fluides (air comprimé, moteurs des procédés, climatisation et éclairage). Le gaz, essentiellement utilisé pour le chauffage du bâtiment, pèse 25% des consommations et l’eau chaude sanitaire 11 %.
Quatre chantiers prioritaires pour réduire les consommations d’énergie
L’entreprise, qui était déjà passée à l’éclairage Led, a ciblé quatre grands chantiers. Ce sont les pertes d’air comprimé, la climatisation, le chauffage des locaux et l’aspiration. Les deux premiers ont été engagés sur l’année 2019, les deux suivants sont programmés en 2020.
«L’enjeu de l’optimisation de nos utilités apparaissait moins prégnant il y a quelques années, dans la mesure où l’usine tournait en continu, 24 heures sur 24, sept jours sur sept. Aujourd’hui, le gros de la production se fait en journée et en dehors du week-end. Par ailleurs, la totalité des installations ne tournent pas en même temps», éclaire Manuel ALONSO.
Les pertes en air comprimé sont généralement évaluées à 30 % sur un réseau industriel. L’effort s’est donc porté sur la réparation d’électrovannes défectueuses afin de mieux isoler les machines à l’arrêt, ainsi que sur des actions curatives en vue de réduire les fuites et l’investissement dans un nouveau compresseur à vitesse variable avec Saft. Le gain a représenté 44 % de la baisse de consommation électrique totale en 2019.
Cette même logique conduit à planifier cette année l’optimisation du réseau d’aspiration. La fabrication d’accumulateurs nickel-cadmium et nickel-métal-hydrure implique en effet la découpe d’électrodes et leur spiralisation dans des machines fermées. La libération de poussières de métaux-lourds lors de ces opérations nécessite leur aspiration dans un réseau alimenté par deux dépoussiéreurs de 40 000 m3/h et 50 000 m3/h chacun, ainsi que d’un aspirateur centralisé (5000 m3/h). La mise en place d’électrovannes permettra d’isoler les machines à l’arrêt suscitant un gain énergétique à deux niveaux : l’alimentation électrique des centrales de dépoussiérage et le chauffage des locaux. En effet, le système de dépoussiérage, dans son schéma de fonctionnement actuel, renouvelle le volume d’air complet des ateliers toutes les 53 minutes !
Le chauffage/climatisation a également été optimisé par la programmation d’arrêts automatiques des pompes à chaleur et des climatisations le week-end. La mise en place de variateurs de vitesse sur les systèmes de ventilation des centrales de chauffage devrait encore permettre des gains supplémentaires. «L’abaissement de la fréquence de 45 à 50 hertz réduira la consommation électrique d’un quart», rappelle le responsable maintenance.
Enfin, la climatisation constitue un poste de consommation important à la fois pour le confort des salariés, mais également pour conduire les tests électriques dont les cycles de charge et de décharge suscitent des dégagements importants de calories. Dans ce domaine, les actions se portent sur le remplacement de deux groupes “froid” par des équipements modernes intégrant la récupération de chaleur. «La mise en œuvre de ce type de groupe froid demeure fortement appuyée par le dispositif des certificats d’économies d’énergie (CEE) qui contribue à leur financement à hauteur de 80 %», pointe Michel Nguyen, ingénieur en alternance chez Arts Energy, associé à l’équipe énergie.
Afin de mener à bien sa certification, l’entreprise a bénéficié du soutien du programme PRO-SMEn, programme national qui incite les entreprises à mettre en place un système de management de l’énergie en leur accordant une prime, une fois le certificat ISO 50001 obtenu. Les entreprises de toutes tailles et de tous secteurs peuvent bénéficier de la prime qui s’élève à 20 % des dépenses énergétiques annuelles des sites certifiés.
* La directive européenne sur l’efficacité énergétique transposée par la loi n°2013-619 du 16 juillet 2013 concerne les établissements de plus de 250 salariés, mais aussi les établissements cumulant un chiffre d’affaires supérieur à 50 millions d’euros et un bilan de plus de 43 millions d’euros. Les sociétés qui adoptent l’ISO 50001 sont exemptées de l’audit énergétique obligatoire.
L’équipe énergie aux commandes
Chez Arts Energy, la démarche de certification ISO 50001 a été entièrement pilotée en interne, par l’intermédiaire d’une équipe “énergie” de cinq personnes, associant les services Industrialisation, Maintenance et Qualité, sécurité, environnement (QSE).
L’animation de l’équipe est assurée par Sarra Berkai, une alternante en formation de responsable QSE au CESI (École d’ingénieurs) d’Angoulême. «Parallèlement à la démarche de certification, il nous est apparu essentiel de développer les compétences de salariés en matière de management des énergies. C’est pourquoi, avec la responsable des ressources humaines, nous avons recherché des programmes de formation adaptés», pointe la responsable de l’équipe énergie.
Arts Energy a identifié le programme de formation des référents énergie dans l’industrie Proferei, développée par l’ATEE. «Les deux jours de formation en présentiel et 20 heures d’accompagnement en entreprise ont permis de structurer notre démarche, d’apprendre à déployer une culture de l’efficacité énergétique en communiquant davantage auprès des salariés et de construire un cahier des charges afin de recruter des prestataires performants en matière d’efficacité énergétique», détaille Manuel Alonso, le référent énergie de l’entreprise. Trois personnes ont d’ores et déjà suivi ce cursus.